Comparing MIG vs. TIG Welding Wire: Which is Better?
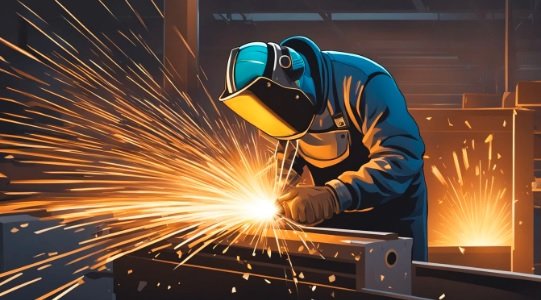
Introduction:
The type of welding wire you opt for can many times make a huge difference in the quality of your work in the welding world. MIG (Metal Inert Gas) and TIG (Tungsten Inert Gas) welding wires are two of the most popular. Each comes with their own set of properties but both are two very different classifications which is important to know in order to choose the right welding wire for the job. This article will take a closer look at the benefits and drawbacks of MIG welding wires vs. TIG welding wires and which of the two you should get based on your particular needs.
Find more information about welding wire and welding techniques at UDO website – https://www.udo.co.th/
MIG Welding Wire:
One of the most frequently performed types of welding in home shops, custom sheet metal fabrication shops, and auto repair shops, is MIG, or GMAW (Gas Metal Arc Welding). MIG welding wire is fed through a welding gun in a process which creates an arc between the wire and the workpiece. Some of the features of MIG welding wire are as follows:
- Although if you are looking to Increase your welding speed: MIG welding would always be faster than TIG Welding So the convenient speed of MIG welding can make it more appropriate for production work where large numbers of assemblies need to be welded.
- All-position welding: This means that this type of welding can be used in all positions like flat, horizontal, vertical and overhead, providing more flexibility.
- Easier to master: MIG welding is often the go-to option for beginners, as it does not need as delicate a touch to maintain a consistent arc length.
- The wires for MIG welding are available in many alloys and grades, including carbon steel, Read the rest
TIG Welding Wire:
This welding process is called TIG welding (Tungsten Inert Gas Welding), GTAW (Gas Tungsten Arc Welding) and it is famous for its accuracy and quality welds. TIG welding uses a tungsten electrode to create the arc with the workpiece being welded, but a separate filler rod is manually provided and added to the weld pool. TIG Welding Wire Weapon Features
- TIG Welding Advantages Superior weld quality: TIG welding delivers the highest standard of weld quality without spatter and virtually without distortion, so it is particularly suitable for critical finishes or joints.
- Control: With a TIG, you have much greater control of the welding process allowing you to fine tune your heat input and filler metal addition.
- Type: Much like MIG welding wires, TIG welding wires are available in several different materials from mild steel, stainless steel, aluminum, and even exotic alloys.
- More time-consuming process: TIG welding is typically slower than MIG welding, so it is better suited for applications where good quality is more important that quick completion.
Selecting The Appropriate Welding Wire
In summary, whether to use MIG or TIG wire depends on your project requirements. Here are a few key to keep in mind:
- Use Case: If you want the fastest production times possible, you might want to MIG welding wire in your welding setup instead. This TIG welding wire may be the best choice if you value the accuracy, look, and welding quality.
- Your material: Make sure that the welding wire matches the material you are welding in the case of mild steel, stainless steel, aluminum or whatever alloy you are using.
- Skill level: If you are new to welding, you might find it easier to use MIG welding wire because there is less precision involved in maintaining an even arc length.
- Applicable specifications for the project Take into account the actual project requirements, such as tensile strength, corrosion resistance and appearance when welding wire for project.
Summary:
In welding, the type of welding wire you use can make a big difference in not only the quality but also the speed of your work! MIG welding wire has faster welding speeds and the ability to weld in all positions, making it better for production work. Meanwhile, TIG welding wire offers high-quality weld appearance, & a greater degree of control, & is widely used in highly cosmetic or industry-required physical integrity applications. In the end, the choice of MIG welder wire vs TIG welder wire will depend on the application, material, skill level and project requirements. Now that you know the strengths and limitations of each type of welding wire involved in the comparison, you can use them as a guide to decide which one will be most beneficial to you.